Bambu Lab’s newly released H2D hybrid 3D printer has stirred widespread discussion across the industry. Recently, Dr. Taoye, CEO of Bambu Lab, sat down for an in-depth interview with popular international YouTuber CNC Kitchen, where he shared the development logic, technological breakthroughs, and future roadmap for the H2D. Based on this interview, we’ve summarized the key highlights for your reference.
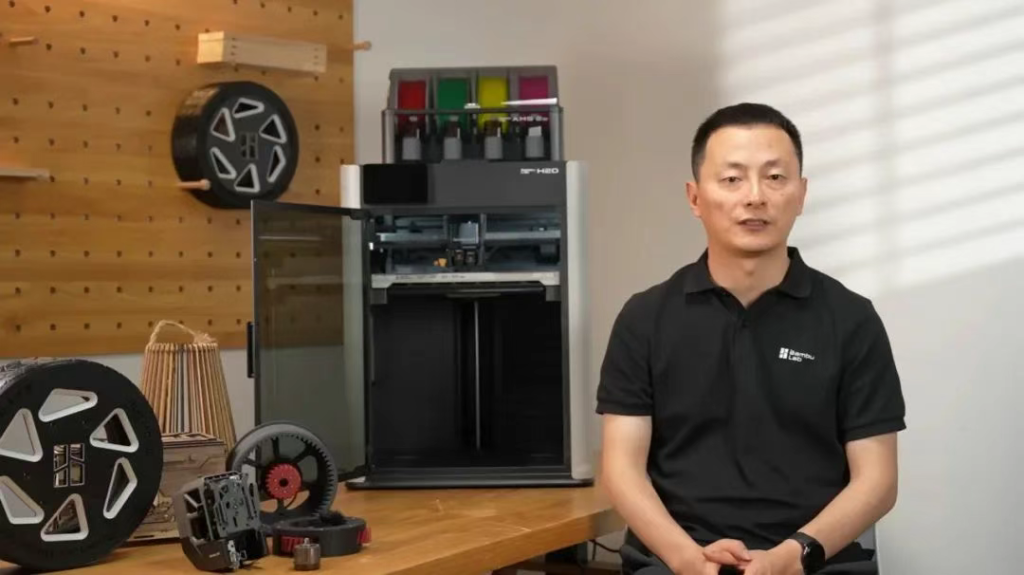
Bambu Lab CEO Dr. Ye Tao
What does the name H2D mean?
H2D is a multifunctional 3D printer that integrates laser engraving, blade cutting, and plotting functions. The letter “H” stands for “Hybrid” or “Hyper,” representing the fusion of multiple capabilities in this flagship product. The number “2” denotes it as the second generation, and the letter “D” refers to its dual-nozzle design.
Why was the product launch delayed?
The delay was primarily due to the complexity of the tool head, structural design challenges, and software development. The dual-nozzle system and laser module required the tool head to be compact and lightweight—every additional centimeter in size increases the machine’s overall volume and weight, which in turn affects printing precision and stability. Complications also arose from vibrations, motor noise, and gear inaccuracies.
Moreover, H2D’s software system is more complex than that of its predecessor, the X1C, demanding extensive physical testing and optimization. During development, the H2D underwent five to six complete iterations, with around 1,500 different prototypes built for internal testing.
Who is the target user for H2D?
Many projects require a combination of manufacturing processes—like 3D-printed structural parts paired with laser-cut decorative elements. Traditional single-function machines often fall short in such cases. H2D follows a “3D printing first, laser/cutting secondary” design philosophy, aiming to reduce users’ equipment costs and save space.
In short, H2D is still a consumer-grade 3D printer at its core, not a machine aimed at professional laser users.
Will the laser affect print quality?
After over 500 hours of laser engraving testing, H2D’s motion system showed no loss in precision due to smoke or dust accumulation. Its linear rails use ball bearings, which provide stronger resistance to particulates and contamination. For materials like wood and paper, the pollutants generated are far less severe than people assume. Users are encouraged to try and judge for themselves.
Additionally, the printer will prompt users for regular cleaning based on usage time and activity.
How is laser safety ensured?
User concerns around laser use mainly involve smoke, dust, and fire hazards. H2D addresses these with five flame sensors, flame-retardant materials, and an air-assist system. A CO₂ fire extinguisher module is also planned for future release.
Lasers can also pose risks to the eyes, so H2D uses a specially treated enclosure and anti-misoperation features. A door sensor cuts off the laser automatically when opened. Emergency stop buttons and a physical local start key add extra layers of operational safety.
Why choose a dual-nozzle design?
Instead of the more common IDEX or toolhead-switching setups, Bambu Lab opted for a dual-nozzle switching design. This approach eliminates waste typically generated during multi-material switching, and supports different materials with varying temperatures and hardness levels.
By using a motor-controlled direct-drive extruder, they can better manage the tool head’s weight and volume.
Why use servo motors?
For extruders, high torque is preferred—stepper motors tend to lose torque at high speeds. That’s why Bambu Lab chose permanent magnet servo motors, which maintain torque regardless of speed.
In addition to powering the extruder, servo motors act as sensors, providing internal pressure data. This allows for real-time nozzle clog detection and flow compensation calibration, leading to significantly improved print quality.
Why not use servos on all axes?
Servo motors are used in the extruder because it requires both torque and precise pressure feedback for stable, accurate printing. For the X, Y, and Z axes, although servo motors could improve precision, factors like pulley elasticity, idlers, and timing belt slack reduce their effectiveness in those areas.
Instead, H2D uses a visual encoder board, where a micro camera mounted on the tool head scans for movement errors and compensates accordingly.
Why not make a larger printer?
Larger machines are harder to control in terms of print quality. They also consume more power, take up more space, and are more difficult to move or ship. After careful analysis, Bambu Lab concluded that a 320mm print volume satisfies the needs of most users.
Going beyond that (400–500mm) would make the machine excessively large. Unless strong market demand arises, the current size is deemed optimal.
Will second-generation technologies trickle down?
H2D is the first machine to feature Bambu Lab’s second-generation technology. In the coming months, H2D’s firmware will continue to be optimized, as there is still plenty of room for refinement.
Eventually, features like servo motors and visual calibration will be introduced to other models. Many new innovations are also in the pipeline for future machines.
What’s Bambu Lab’s stance on previous open-source controversies?
Regarding past controversies over firmware updates and open-source issues, Bambu Lab never officially promoted the MQTT protocol nor claimed to have fully opened it.
As a compromise, the developer mode remains available, allowing advanced users to customize their devices. However, regular users are still encouraged to stick with the default settings for a stable, safe, and reliable experience.
Additional insights from the interview Dr. Taoye also shared a number of exciting updates:
- MakerWorld will launch more 2D files suitable for engraving, cutting, and plotting.
- MakerLab will soon support corresponding 2D file generators.
- Accessories like rotary modules for laser engraving are coming, but there are no plans for a CNC cutting module.
- The current AMS system cannot yet feed both extruders simultaneously, though this may change.
- In the future, different nozzle sizes may be supported, pending software improvements.
- CyberBrick, a new modular building block ecosystem, is on the way—for applications like RC cars and model aircraft.
These insights were all shared during the recent interview. The release of H2D marks more than just the launch of a new machine—it represents a redefinition of home-based manufacturing capabilities.
Whether hybrid manufacturing can evolve from a niche hobbyist trend into a mainstream market remains to be seen, and we’ll be watching H2D’s performance closely.
Lastly, we realized that being an outstanding content creator requires not only professional knowledge but also a strong set of personal values and convictions. Perhaps that’s one reason Bambu Lab chose CNC Kitchen for this interview out of the sea of creators.
Leave a Reply